Machine Identification
Even the most advanced and precise CNC machine tools cannot be expected to execute perfectly NC paths generated by CAM software. To achieve ultra-precise surfaces, we have found it necessary to identify all aspects of both static and dynamic machine errors. We are still actively researching the influence of geometrical errors on the material removal rate of compliant grinding and polishing tools.
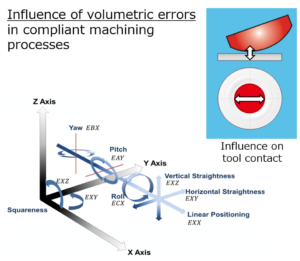
Sustainable Manufacturing
Machine tools contribute up-to 50% of energy use in manufacturing. As surfaces become closer to the final finish, the specific energy needed for further improvement increases exponentiall. Consequently, optimization of process steps is crucial not only to overall process time but also to the efficient use of energy in manufacturing of precision components. Machining processes (cutting, grinding, polishing, etching, deposition, etc.) generally associate a set of inputs (substrate material, tool, etc.) with outputs (modified material, added/removed volume, surface finish, etc.). This commonality of behavior facilitates the abstraction of machining processes as causal operators. Abstraction offers several benefits, such as the ability to rationalize monitoring of inputs/outputs as function of energy expended, but also the possibility of recording the associated data within a generalized database schema (linked tables for material properties, surface properties, energy use, etc.).
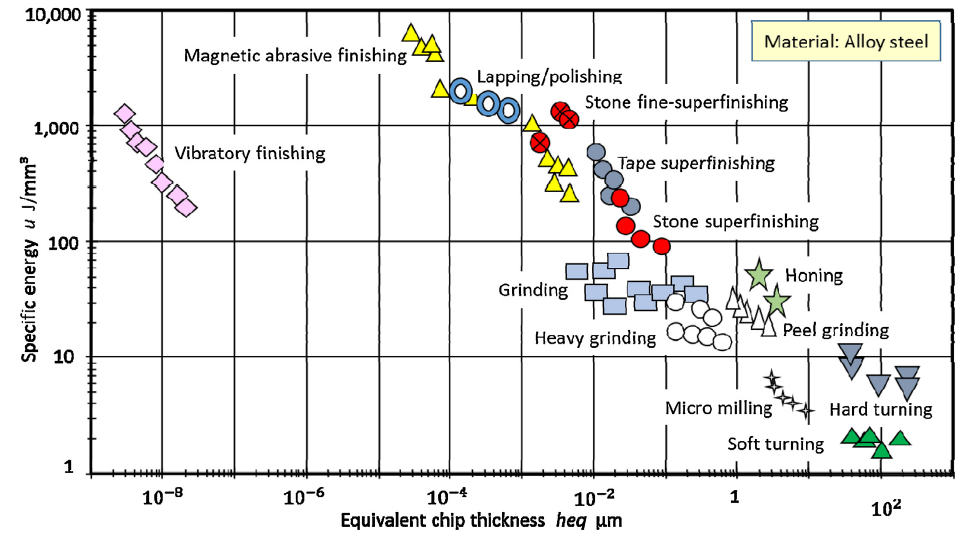