Controller Identification
Many additive, subtractive, and material modifying processes are time dependent. Accurately simulating and controlling such processes involves several tasks: predicting surface properties by convoluting the process influence function and tool path characteristics, locally adjusting toolpath tracks to improve these properties, and scheduling feed-rate while taking into account machine and controller dynamics.
Once the polishing part program is inputted to the machine tool, it is first processed by the NC system, which interpolates the G-code and generates reference motion commands (trajectories) to the feed drive axes of the machine tool. The dynamic accuracy of machining during contour process operation is affected primarily by:
- The interpolation (trajectory generation) accuracy of the NC system.
- The command tracking performance of feed drive axes of machine tool.
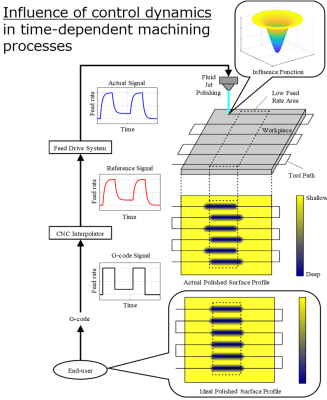